Wow thanks for all the help and advice!
I headed down to Chan Man Lee during lunch upon the advice of Wongster to get a new B16 drill chuck, I've attached a photo of it. It's of much more substantial construction than the previous one, being of solid steel construction. I'll check the runout tomorrow.
Apparently the B16 taper is a German taper, having the same taper to length ratio as a morse taper, just shorter. Also, I forgot to add that it's a protruding arbour, and not a typical internal taper on normal mills.
I think I will make do with the chuck instead of troubling others.
Btw, the object in the first photo is the previous mutilated drill chuck
<br> <br>
I headed down to Chan Man Lee during lunch upon the advice of Wongster to get a new B16 drill chuck, I've attached a photo of it. It's of much more substantial construction than the previous one, being of solid steel construction. I'll check the runout tomorrow.
Apparently the B16 taper is a German taper, having the same taper to length ratio as a morse taper, just shorter. Also, I forgot to add that it's a protruding arbour, and not a typical internal taper on normal mills.
I think I will make do with the chuck instead of troubling others.
Btw, the object in the first photo is the previous mutilated drill chuck

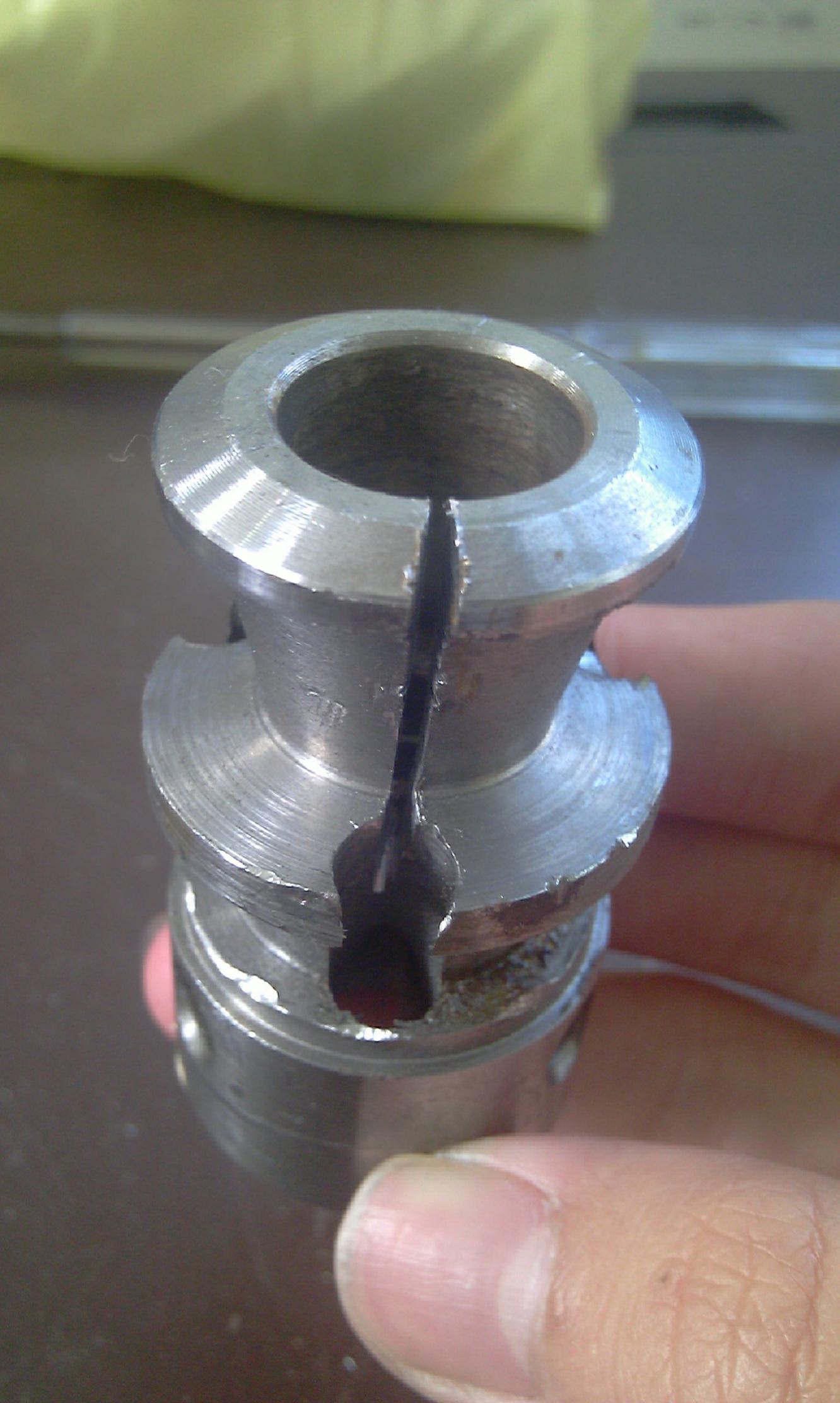
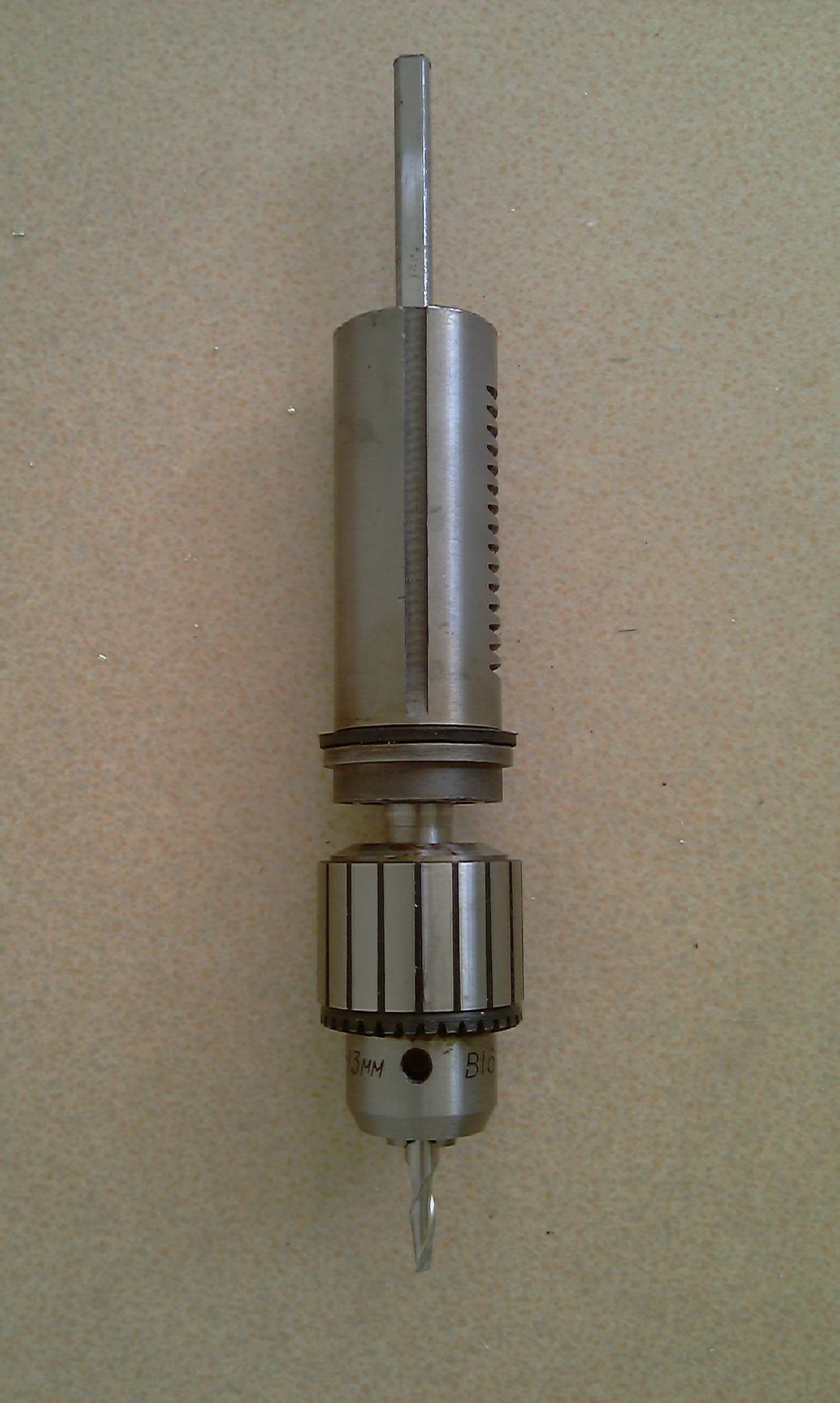
Comment