Thought I'd start this thread to share my project.
Here's what I've been working on in the little spare time I have...
not finished yet.
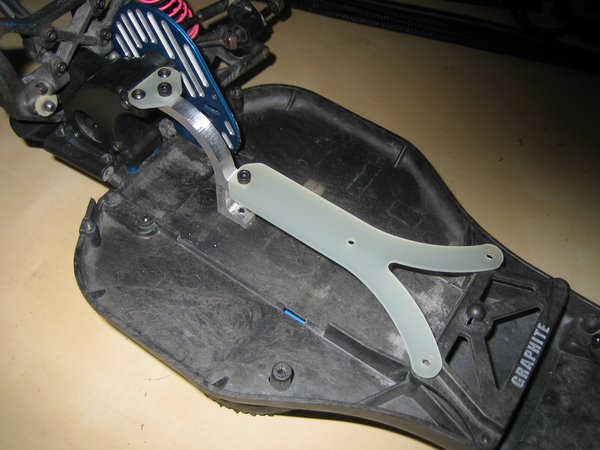
It's a custom modification of a Losi XXX buggy. Just playing around with some ideas and at the same time picking up the basics of CNC.
Many thanks to HZM for his help in getting me started in CNC.
Here's what I've been working on in the little spare time I have...
not finished yet.
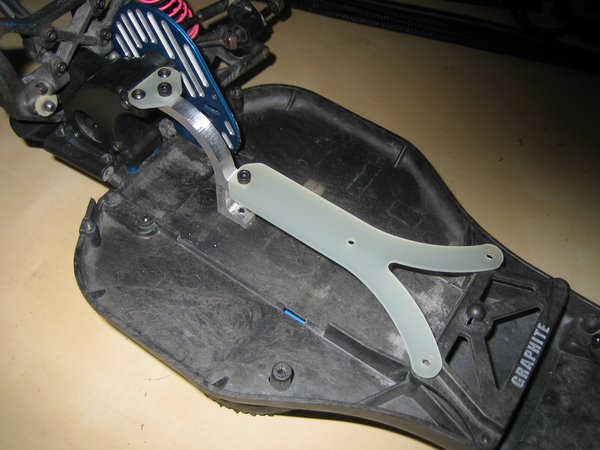
It's a custom modification of a Losi XXX buggy. Just playing around with some ideas and at the same time picking up the basics of CNC.
Many thanks to HZM for his help in getting me started in CNC.

Comment