I re-started this thread for my Cobra-17 for a good reason. This one would be a assembly log as a guide to others who wants or already has the kit. The previous thread was titled something else and I'd think that starting a new thread like this should be easier for the readers.
Just a quick recap, this kit is solely distributed by Staufenbiel in Humburg at the moment and is manufactured in Czech republic by Royal-model. Fuselage is beautifully made of fibreglass, together with the canopy frame. The canopy is moulded from clear plastic. The wings, stabilizer and rudder are balsa built-up and covered in some kind of iron-on covering. Mine has a quite a bit of wrinkles and I have since redo the covering with Oracover. The kit comes with complete hardwares for the model. You'll need radio, battery, and adhesive to complete the model.
The wingspan is 2.6metre, estimated AUW is 1.2 kg. Wing area is 34dm^2 and airfoil is S3010. 3 channel controls ( Ailerons, rudder and elevator) with 4 servos. You can program spoilerons if you wish to.
Just a quick recap, this kit is solely distributed by Staufenbiel in Humburg at the moment and is manufactured in Czech republic by Royal-model. Fuselage is beautifully made of fibreglass, together with the canopy frame. The canopy is moulded from clear plastic. The wings, stabilizer and rudder are balsa built-up and covered in some kind of iron-on covering. Mine has a quite a bit of wrinkles and I have since redo the covering with Oracover. The kit comes with complete hardwares for the model. You'll need radio, battery, and adhesive to complete the model.
The wingspan is 2.6metre, estimated AUW is 1.2 kg. Wing area is 34dm^2 and airfoil is S3010. 3 channel controls ( Ailerons, rudder and elevator) with 4 servos. You can program spoilerons if you wish to.
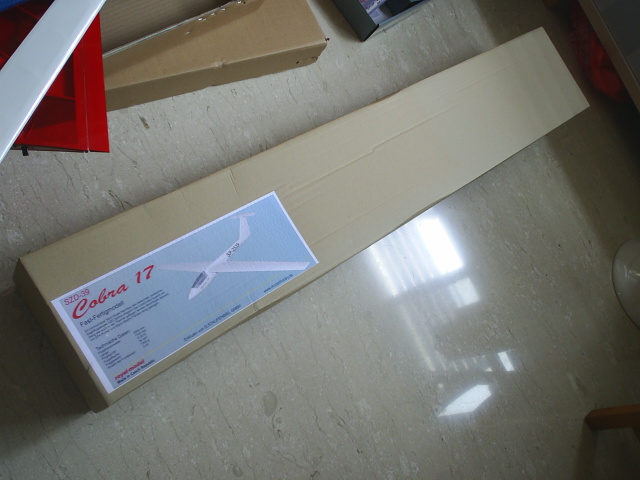
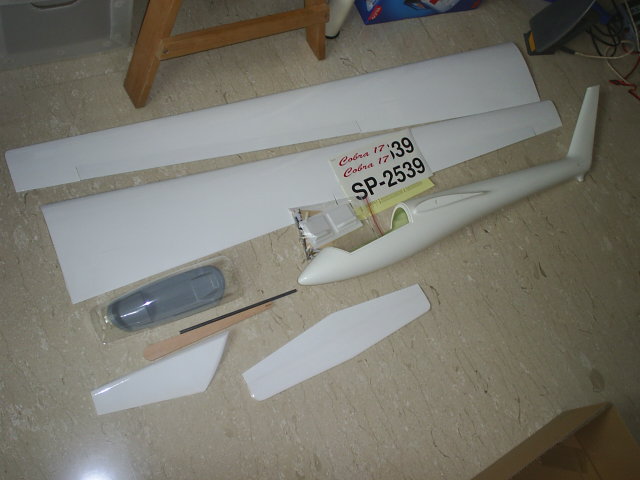
Comment