Need some help to machine two parts for a heli. Material preferably in t7075 aluminium, but if its a lot more ex than 6061 aluminium, I might settle for 6061. So it price pending. Maker will help to supply material.
1 piece of this
45mm long and 12mm in diameter and the flat surface(two sides) has to be grind down to about about 10.9-11mm. 3hole(threaded) to suit a 2.5mm screw on each flat side, a total of 6 holes. A hole(none threaded) of 3.5mm has to go through from end to end with a 7.99mm diameter 4mm thick recess at both end to fit in a bearing each end. <br> <br>
1 piece of this
45mm long and 12mm in diameter and the flat surface(two sides) has to be grind down to about about 10.9-11mm. 3hole(threaded) to suit a 2.5mm screw on each flat side, a total of 6 holes. A hole(none threaded) of 3.5mm has to go through from end to end with a 7.99mm diameter 4mm thick recess at both end to fit in a bearing each end. <br> <br>
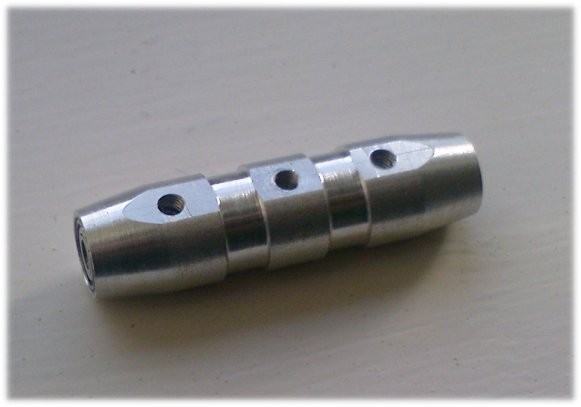
Comment