Tamiya re-released the Top Force some time ago and it's a very nice car to run. 
I hand-milled some aluminum shock towers for the car but because they were done by hand they weren't the prettiest so decided to try something a bit more "factory" looking.
Here's the pic from my CAM program...
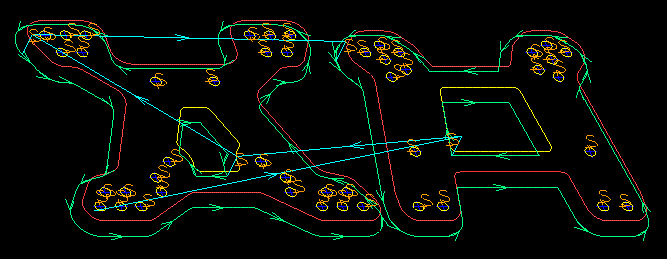
If it rains tomorrow I'll try cutting these out...

I hand-milled some aluminum shock towers for the car but because they were done by hand they weren't the prettiest so decided to try something a bit more "factory" looking.
Here's the pic from my CAM program...
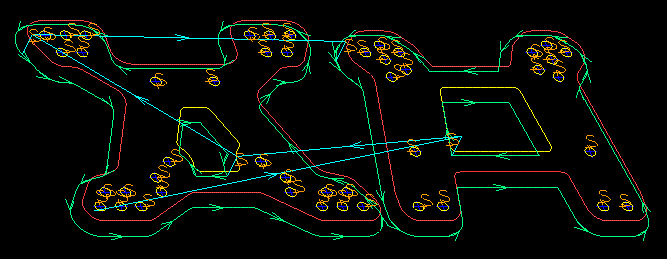
If it rains tomorrow I'll try cutting these out...
Comment