Hi all,
as promised, I'm posting pictures of my new CNC setup. It's still a virgin as I have yet to figured out how to cut my first part. I was hoping someone in this forum could help me out.
The following are the front & back view of the parts that I'm trying to make. The third image show how the part is orientated to be clamped and machine. It's a container to hold 2 RC servo motors. I've got the CAD drawing, I've also generated the g-code. I just can't figure out how to clamp and cut the parts.
Here's are the problems:
1) How do I cut the outer profile, without cutting my milling table, since it needs to cut all the way to the bottom?
2) How do I cut such a deep inner pocket, since the cutting part of my end mill is short and the non cutting part of my end mill will collide with the sides of the inner pocket when it is cutting too deep?
3) My aluminum stock is too long and I do not have a jig or band saw, is there any way of cutting it will my mill? I know it will shorting the life of the cutting tool but I do not have the budget or space for a saw
<br> <br>
as promised, I'm posting pictures of my new CNC setup. It's still a virgin as I have yet to figured out how to cut my first part. I was hoping someone in this forum could help me out.
The following are the front & back view of the parts that I'm trying to make. The third image show how the part is orientated to be clamped and machine. It's a container to hold 2 RC servo motors. I've got the CAD drawing, I've also generated the g-code. I just can't figure out how to clamp and cut the parts.
Here's are the problems:
1) How do I cut the outer profile, without cutting my milling table, since it needs to cut all the way to the bottom?
2) How do I cut such a deep inner pocket, since the cutting part of my end mill is short and the non cutting part of my end mill will collide with the sides of the inner pocket when it is cutting too deep?
3) My aluminum stock is too long and I do not have a jig or band saw, is there any way of cutting it will my mill? I know it will shorting the life of the cutting tool but I do not have the budget or space for a saw

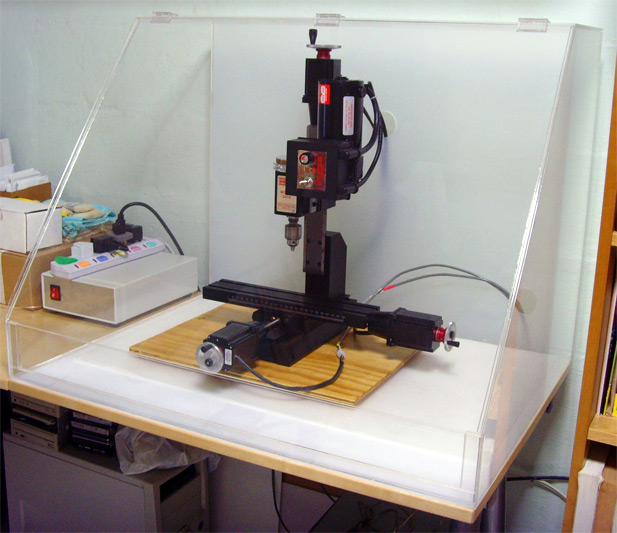
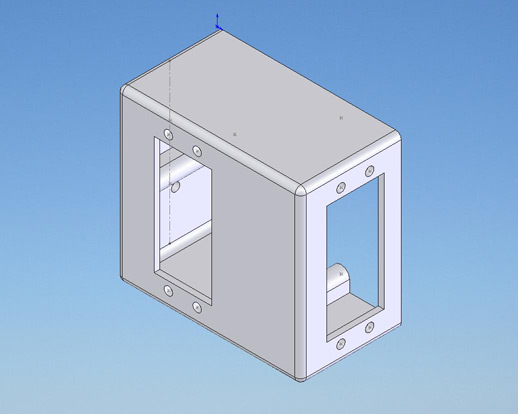
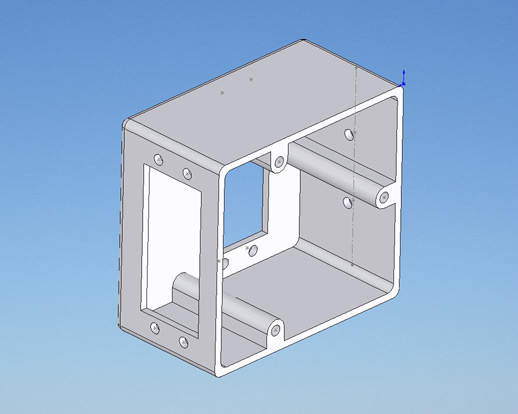
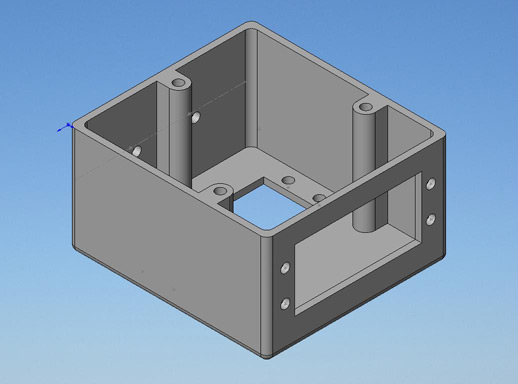
Comment