Time to get started to build something for the forthcoming scale fun fly in November. I thought the Sig 1/5 Cub would be an easy enough build to be ready by then. Having a new and unused Saito 70 made the decision a no brainer.
Typical Sig quality balsa ie. balsa is nice and crisp. None of that soft and weak or super heavy stuff. Quality was very consistent throughout. The laser cutting on this kit is very good. Parts just about almost fall out and fit is very good.

4 rolled plans are provided in the kit. I found out that I had an extra plan no. 3 and was short of plan no. 4. An email to the Sig had the missing plan arriving in a tube in just a little over a week. Good after sales service.
I start by plucking all the parts out and keeping them in zip lock bags.
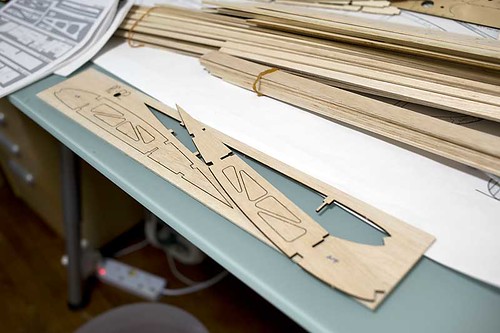
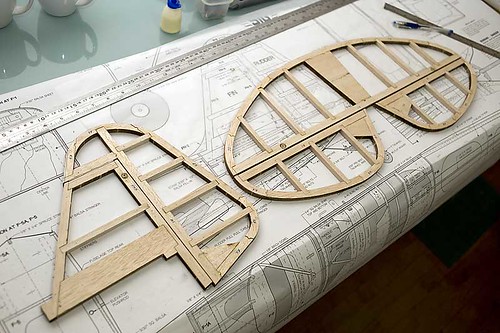
So far, the kit is coming together very quickly. Faster than I thought it would. The excellent parts fit and clear instructions had a part to play in this. I've finished the tail group and should be completing the wing within a week.
Typical Sig quality balsa ie. balsa is nice and crisp. None of that soft and weak or super heavy stuff. Quality was very consistent throughout. The laser cutting on this kit is very good. Parts just about almost fall out and fit is very good.

4 rolled plans are provided in the kit. I found out that I had an extra plan no. 3 and was short of plan no. 4. An email to the Sig had the missing plan arriving in a tube in just a little over a week. Good after sales service.
I start by plucking all the parts out and keeping them in zip lock bags.
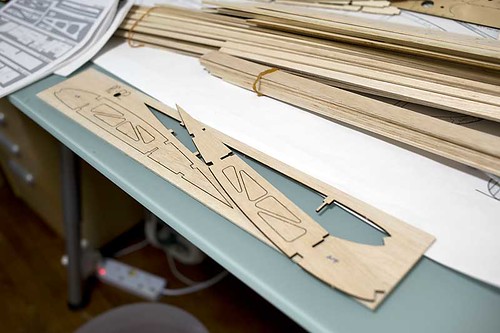
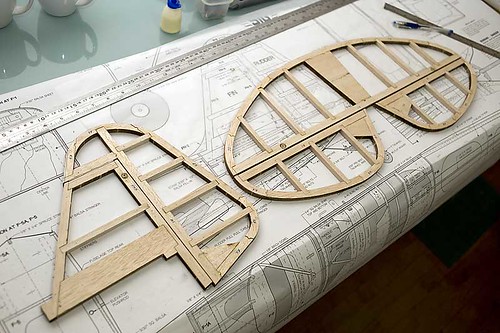
So far, the kit is coming together very quickly. Faster than I thought it would. The excellent parts fit and clear instructions had a part to play in this. I've finished the tail group and should be completing the wing within a week.
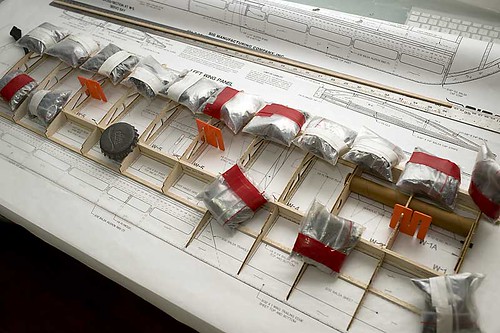
Comment