My hands are itching to scratch build another plane again
and what better plane to build than to build another Tucano. For the 2nd version I'm going make this one as streamlined and rounded as possible. If I got more time I'm going to use this paint scheme of the Peruvian Airforce.
At this stage, the plane is in 3D design stage to see how the foam fits together.
I've already got all the building materials and I'm going to document each stage of my build progress. Stay tuned!

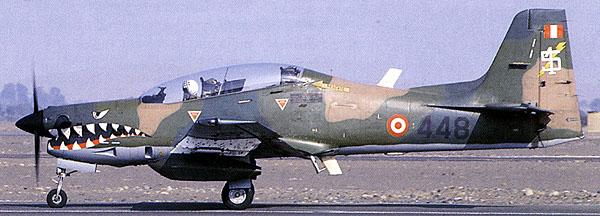
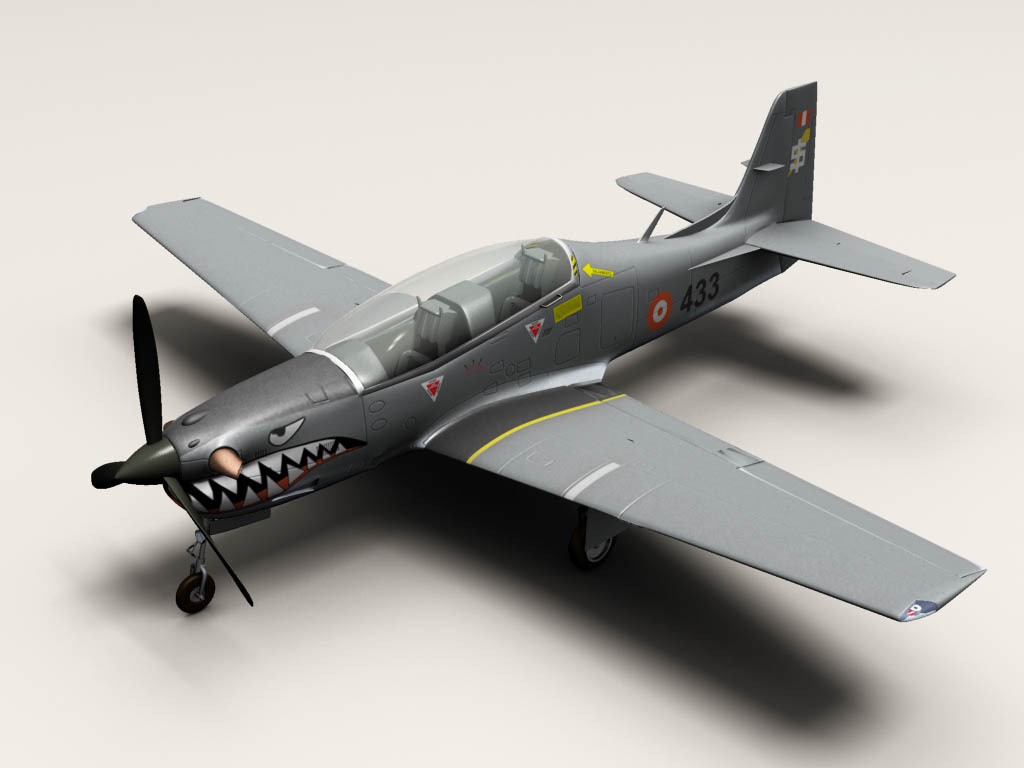
At this stage, the plane is in 3D design stage to see how the foam fits together.

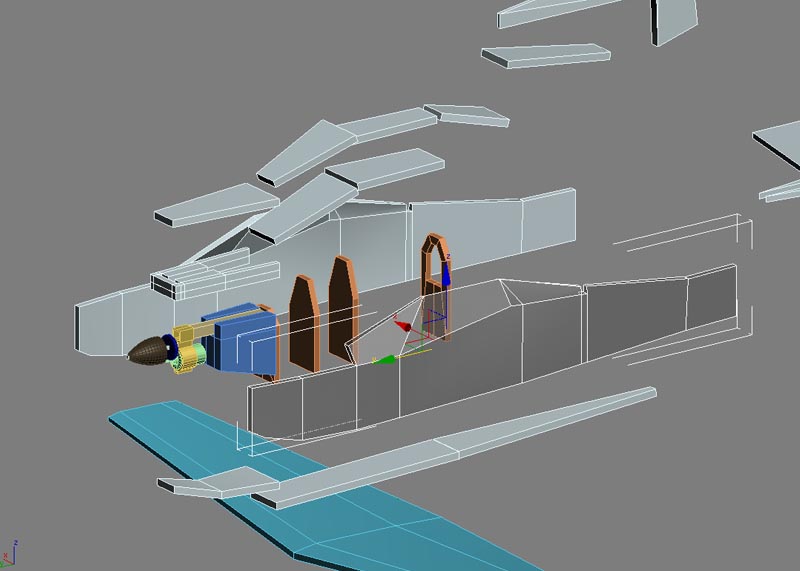
I've already got all the building materials and I'm going to document each stage of my build progress. Stay tuned!
Comment