Due to some numerous response to how to use the Hotwire, I'm going to write not a comprehensive, but a simple mini guide with basic instructions how to use the hotwire to cut out foam parts. For starters, i shall began with "how to cut out a foam wing".
First up, for those who want to DIY their own hot wire cutter, refer to the picture below. All you need is:
1)PVC pipe ,buy at least a 2m long pipe at your local hardware store for a few dollars. Diameter dosen't really matter, of course thicker the stiffer it is
2)Nichrome wire, That will be your heating element, bought from diaso for $2!
3)22-16AWG wires, remember,the thinner the wire the higher the voltage drop! And you'll get no heat out of your nichrome wire if the wires are too thin. Infact,your copperwire will be the one producing heat instead!
4)Crocodile clips, optional but useful to use as a temperature control for non-variable powersupply. The clip can be slide back and forth on the nichrome wire to vary the temperature.
*Note, the temperature depends on 3 things, the temperature will be hotter if:
1)The wire is thinner
2)The wire is shorter
3)More current is flowing through the wire
Similary, if you want to achieve colder temperature, do the opposite.
The dimension of your hotwire depends totally on you. You could build a small cute 50cm long ones or a giant 2m hotwire. But an ideal size would be 100cm long as foam suppliers from artfriend supply common blocks of foam in size of 3ft (91.5cm) x 2ft (61cm) x 2inch (5cm).
Right below is a picture of my DIY hotwire ,not very stylish but it has lasted me for 2years now and still working fine (well,its just some pipes and wires anyways what could go wrong!) The details are in the picture.
I own another 2 other hotwire cutter made of aluminium rods, one longer one (3ft) and short one (1ft). For small detail works i'll use the smaller ones, for general cutting like slicing off huge chuck of foam,the large one will be the preferable choice.
First up, for those who want to DIY their own hot wire cutter, refer to the picture below. All you need is:
1)PVC pipe ,buy at least a 2m long pipe at your local hardware store for a few dollars. Diameter dosen't really matter, of course thicker the stiffer it is
2)Nichrome wire, That will be your heating element, bought from diaso for $2!
3)22-16AWG wires, remember,the thinner the wire the higher the voltage drop! And you'll get no heat out of your nichrome wire if the wires are too thin. Infact,your copperwire will be the one producing heat instead!
4)Crocodile clips, optional but useful to use as a temperature control for non-variable powersupply. The clip can be slide back and forth on the nichrome wire to vary the temperature.
*Note, the temperature depends on 3 things, the temperature will be hotter if:
1)The wire is thinner
2)The wire is shorter
3)More current is flowing through the wire
Similary, if you want to achieve colder temperature, do the opposite.
The dimension of your hotwire depends totally on you. You could build a small cute 50cm long ones or a giant 2m hotwire. But an ideal size would be 100cm long as foam suppliers from artfriend supply common blocks of foam in size of 3ft (91.5cm) x 2ft (61cm) x 2inch (5cm).
Right below is a picture of my DIY hotwire ,not very stylish but it has lasted me for 2years now and still working fine (well,its just some pipes and wires anyways what could go wrong!) The details are in the picture.
I own another 2 other hotwire cutter made of aluminium rods, one longer one (3ft) and short one (1ft). For small detail works i'll use the smaller ones, for general cutting like slicing off huge chuck of foam,the large one will be the preferable choice.
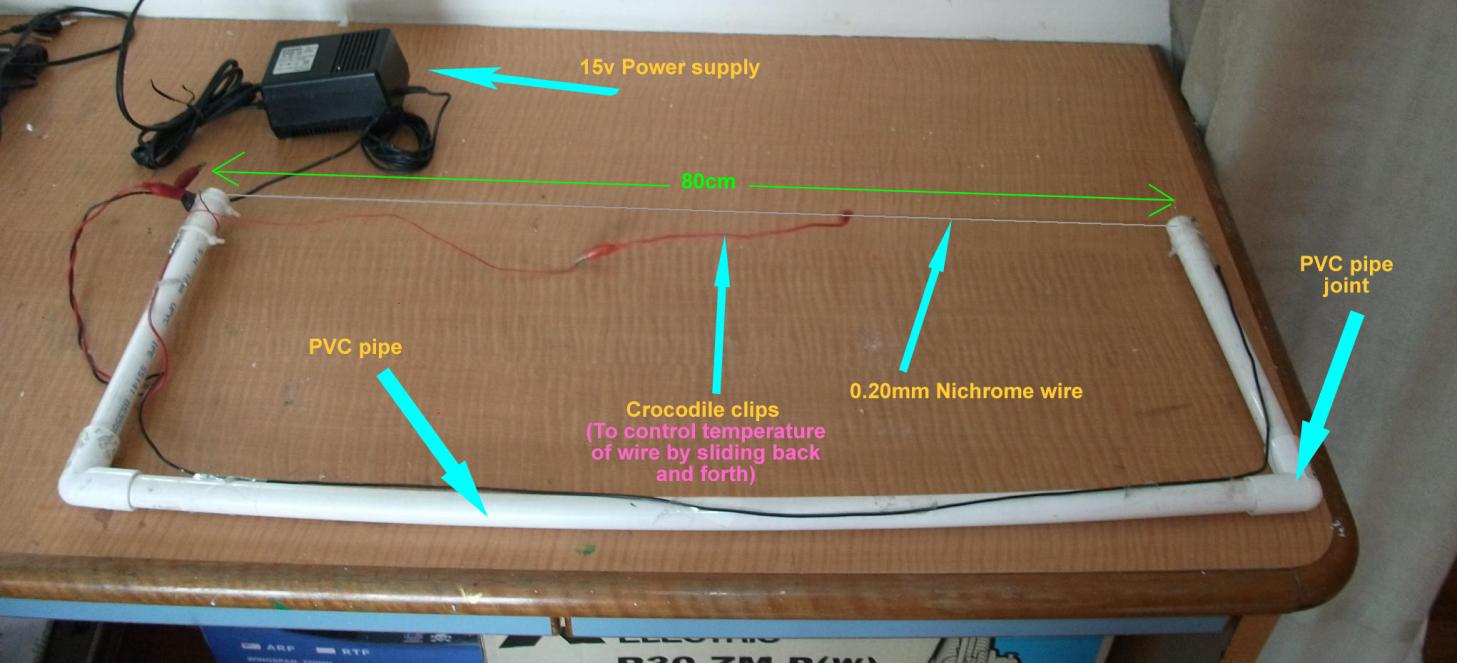
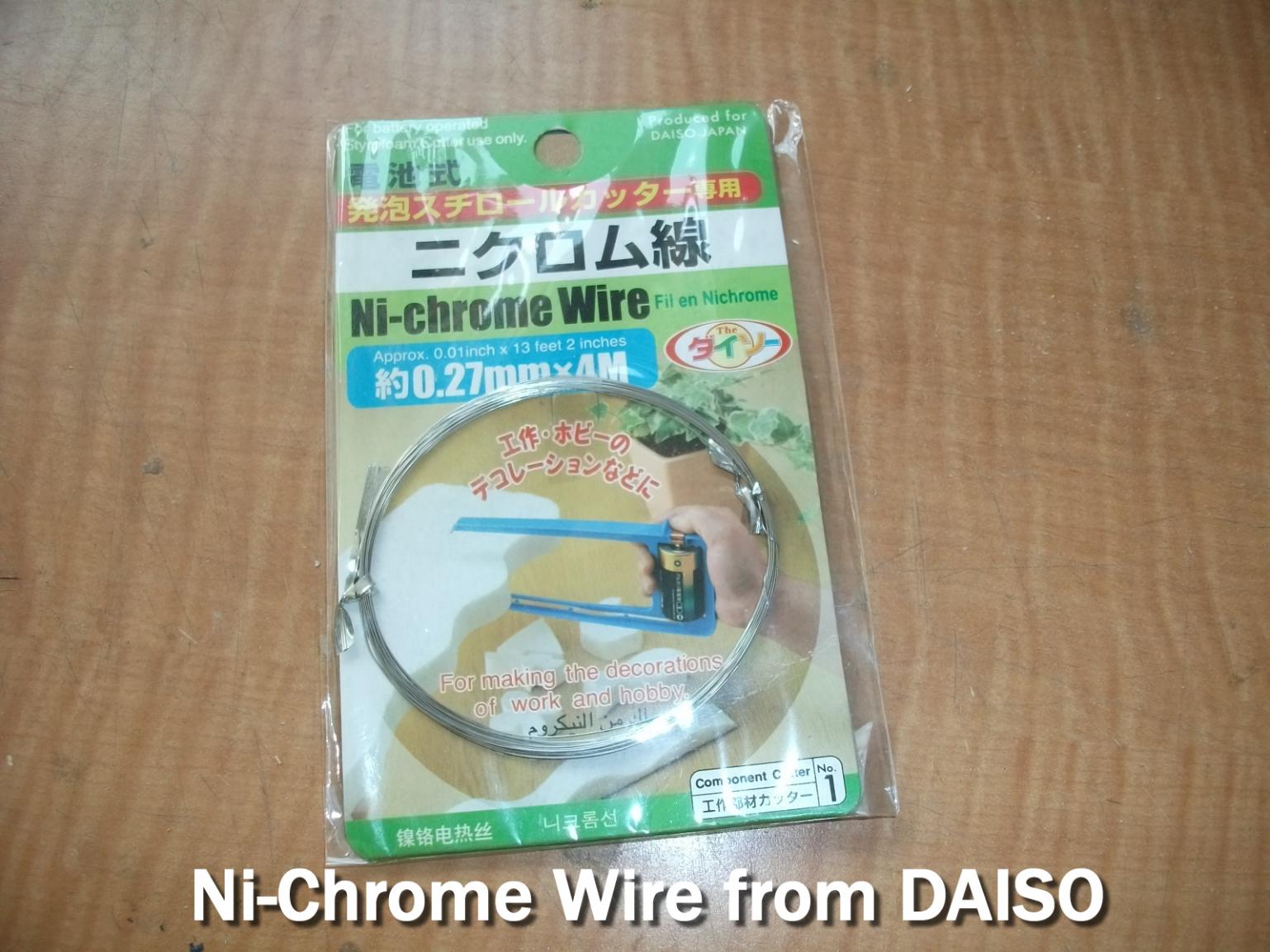
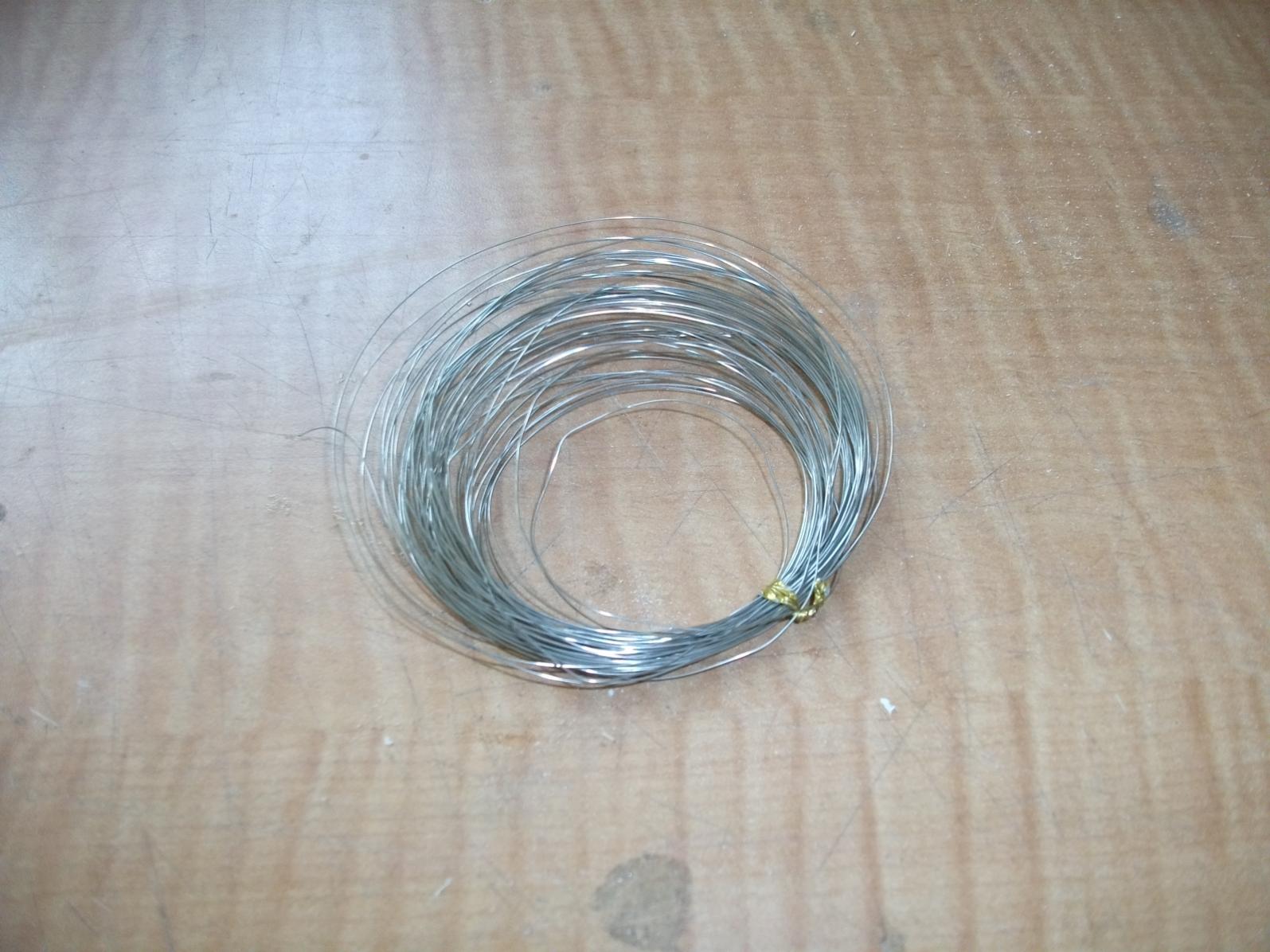
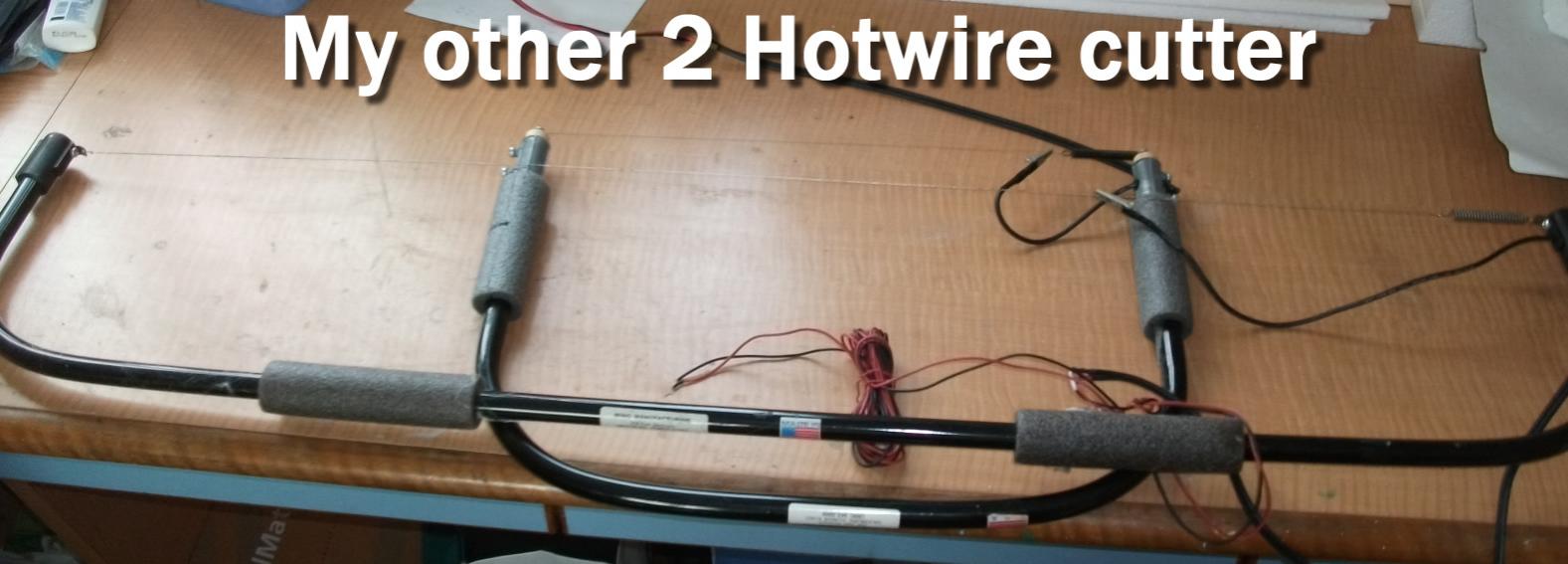
Comment